Cast Iron Welding
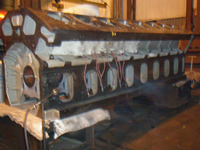
A thorough evaluation of the iron casting area to be upgraded will determine whether the metal stitching process or the welding process will be utilized.
Considerations will involve:- Location of area to be upgraded.
- Effect of the application of heat on casting dimensions.
- Ability to preheat.
- Type of upgrading to be performed (cracking, lack of stock etc.)
- Economics of metal stitching versus welding.
If the decision is made to weld, and material specifications are not available, a metallurgical analysis will be preformed and proper procedure written. The welding procedure generally used is that listed in American Welding Society’s Standard D11.2-89, “Guide for Cast Iron Welding”. Certified welders will perform the necessary upgrading.
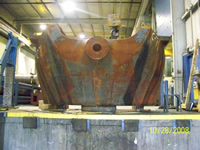
Preheating is applied with a confined heating area, torches or ceramic heating pads (electrical). Welding modes are SMAW, GMAW, or FCAW (Shielded Metal Arc, Gas Metal Arc, Flux Cored Arc).
When post-heating or stress relieving is required, ceramic heating pads generally are used.
All welds are ground to conform to the base metal contour and are inspected visually and/or using the inspection techniques of liquid penetrant and magnetic particle testing.